Jetztertle!
Hat dann doch noch etwas länger gedauert, da ich gestern doch noch einiges an fine-tuning bei der Passform der Bleche vornehmen mußte. Idealerweise nehmen alle Bleche ihre Position ein, ohne daß man sie da irgendwo hin drücken / biegen muß. Da das noch nicht überall so war, habe ich dann doch noch einiges an Arbeit investiert und habe die Bleche weiter geglättet, gebogen etc. ... - was halt so notwendig war um alles in nahezu optimaler Passform hin zu bekommen.
Das Heckblech konnte ich gestern auf der Beifahrerseite schonmal anschweißen. Links fehlte noch die hintere Ecke vom Radhaus, die ich ja vor einer Weile schonmal grob vorbereitet habe unter Verwendung eines aus einem geschlachteten Saab 96 gewonnen Radkastenblechs.
Da dieses an der Vorderkante an den Rest vom originalen Radhausblech anschließen sollte, mußte ich da noch einige Anpassungen vornehmen. Am Ende zeigte sich, daß die Lücke zu groß war um sie zu zu schweißen.
" 3 Mal abgeschnitten und immer noch zu kurz..."
Also habe ich einen ca. 10cm breiten Blechstreifen in die Sickenmaschine gesteckt und habe die Sicke ins Blech gerollt. Das Stück habe ich dann ca. 10cm weiter vorne angesetzt. Das alte Stück war zwar schonmal von mir gerichtet worden (war zerknittert von dem Heckschaden hinten links), aber das war immer noch nicht so richtig gerade und außerdem teilweise arg dünn. Da hatte ich starke Bedenken daß mir beim anschweißen das alte Blech einfach weg brennt.
So bin ich bequem im gesunden Bereich gewesen und konnte das Blech entspannt ansetzen. Dann habe ich das hintere, neu angefertigte Stück vom Radhaus rein geklemmt und habe es mit ca. 5cm Überlappung auf das neu angesetzte Stück Blech mit Clecos rein gesetzt. Dann einen Schnitt durch die Überlappung und schon hat man eine perfekt passende Kante zum anschweißen.
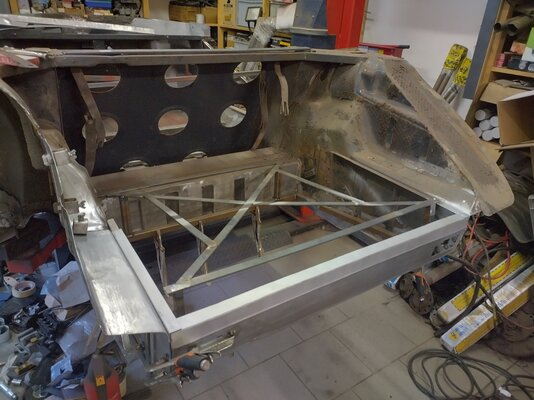
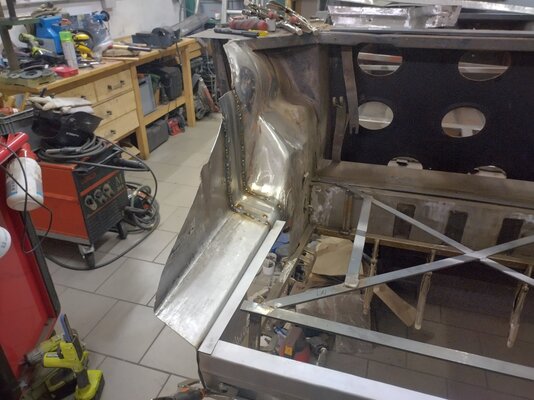
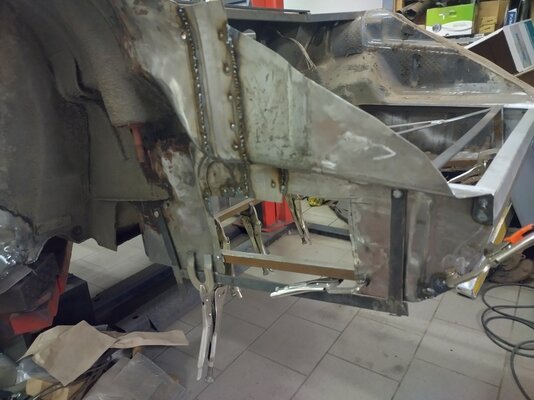
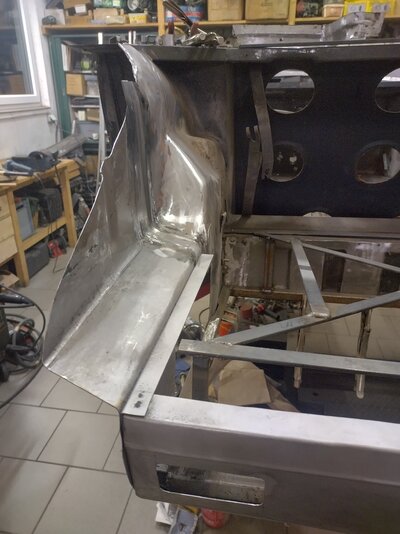